Feltrin+Masarin’s Swing Door is testament to the brand’s perfect precision
Discover the mastery of metalwork that goes on inside the impressive reproduction facilities of Italian metal manufacturer, Feltrin+Masarin.

Last year, we were lucky enough to be invited inside the multidimensional industrial reality that is Feltrin+Masarin, the Italian brand, which has over forty years developed, industrialised and produced innovative metal components for companies seeking the highest quality in product and service.
The company specialises in the processing of metals, hence our initial interest in the Sign Filo chair, a complex construction made from steel wire totalling 45 metres.

This time around, however, we’ve decided to take a look at something a little different—a swing door that Feltrin+Masarin manufactured for a major tech brand’s ultra-minimalist offices.
Demonstrating Feltrin + Masarin’s ability to manage and manipulate aluminium, the product is the outcome of a painstakingly careful process at the brand’s 7,000 square foot production facilities based in the heart of Veneto in the northeastern region of Italy.
Here, a dedicated centre specialises in the production of doors bringing together craftspeople and mechanics with 40+ years of experience and 2 generations at the service of Italian creativity.
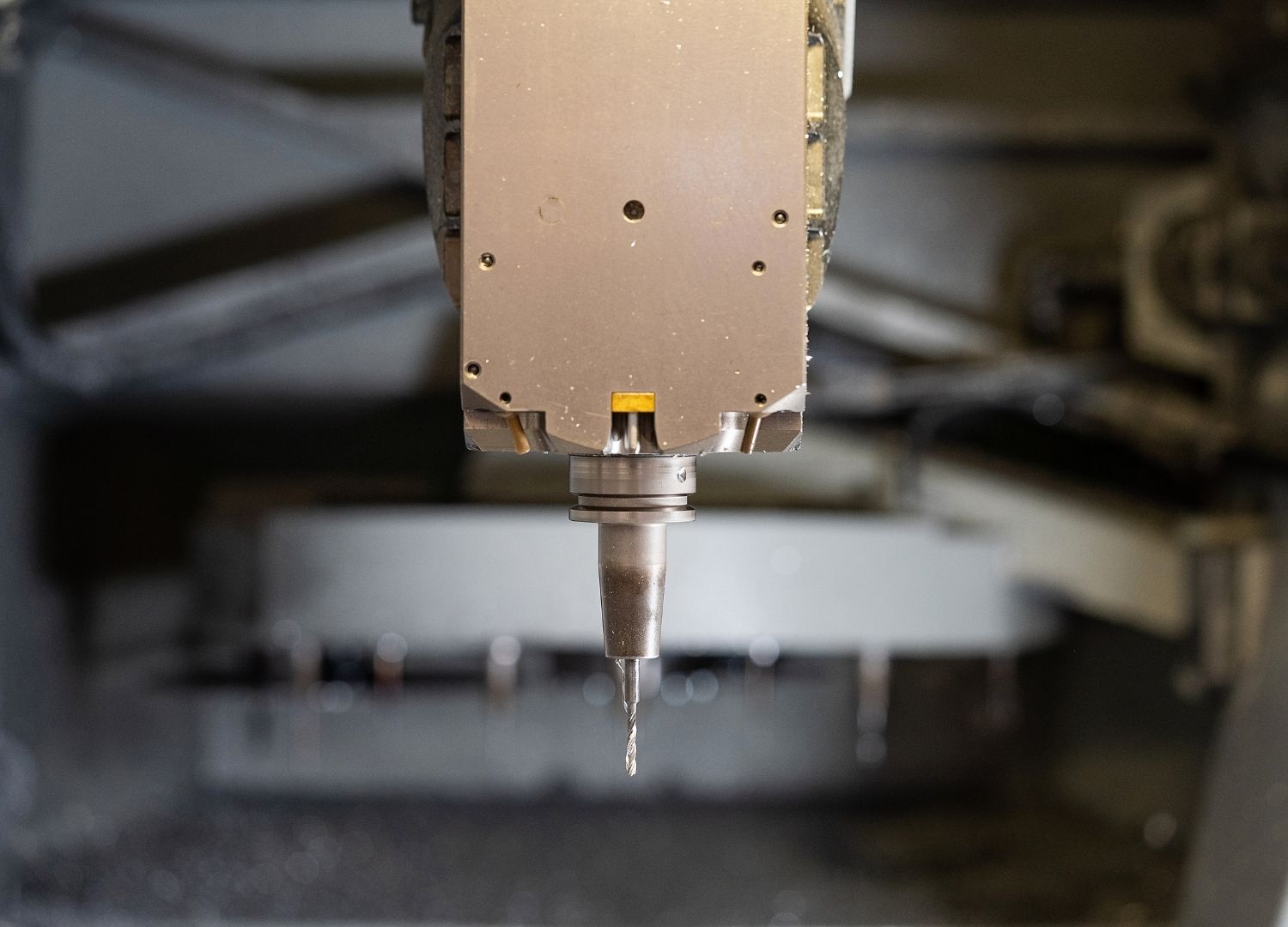
“This project, which we carried out for an important brand in California, has allowed us to improve the industrialization process,” explains Feltrin + Masarin.
“We have come to produce about 5,000 doors in 2 years, and with this project 3M double-sided adhesive has been definitively introduced as a method of glueing in place of silicone.
The use of double-sided tape has allowed us to create increasingly more design projects and has opened the doors for us to collaborate with high-level architects.”
Here, Feltrin+Masarin gives us another inside look at these facilities, this time with a step-by-step breakdown of the Swing Door’s production (see below)…
Phase 1: quality control
After receiving the glass panels and selecting the correct profiles, the first action Feltrin + Masarin takes is a preliminary quality control.
“In the first phase, the profiles, painted, coated or anodized, are placed in the cutting machine [but first we have to ensure each component is as expected, checking for dents, smears or any other imperfections],” explains Feltrin + Masarin.

The cutting machine uses a 550-millimetre super high speed steel (HSS) blade with cemented carbide teeth to perform inclined cuts anywhere between 22.5 and 90 degrees depending on the profiles used during assembly.
“We use machine software for cutting optimization to ensure as least waste as possible from the profiles),” Feltrin + Masarin adds.

Phase 2: cutting
Next, the profiles are moved and inserted into the 5-axis CNC machining centre — 5-axis refers to the number of directions in which the cutting tool can move.
On a 5-axis machining centre, the cutting tool moves across the X, Y and Z linear axes as well as rotates on the A and B axes to approach the workpiece from any direction.
“During the design phase it is possible to load a 3D model into the machine, which reduces the time spent programming the machine,” says Feltrin + Masarin. “It also makes for greater precision when it comes to operations.”

This enables the machining centre to independently choose which tools it needs, depending on the machining that needs to be carried out: cutting or milling, for example. In addition to the different cutting and milling processes, the machining centre can work on both aluminium and steel extrusions, over a maximum length of 10m.
“There are up to 20 tools available, including blade and cutters of different diameters in solid carbide spherical, flat, multi-flute, insert cutters for roughing and finishing, shoulder, smoothing and copy.”
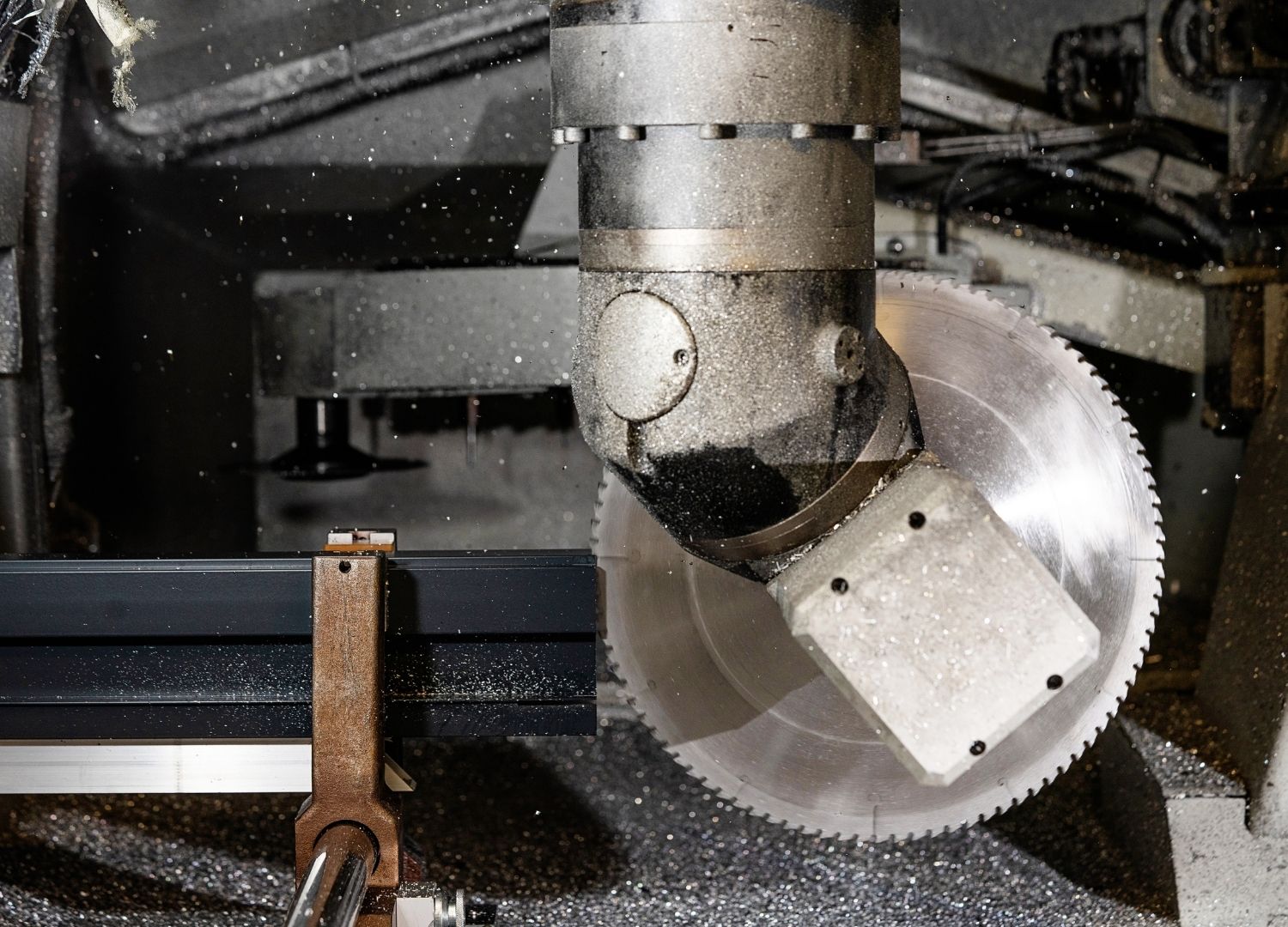
Phase 3: assembly
In Phase 3, assembly requires a thorough cleaning, which is carried out before 3M double-sided tape is placed on each profile with the help of a guide roller.
Here, Feltrin + Masarin has foregone the option of using silicone.
This improves the aesthetics because it is possible to put glass on sight and not recessed “in frames” as with silicone.
The 3M double-sided tape is also used in all processes because the glueing time is reduced to a minimum.

“The skeleton is then assembled by positioning the profiles in bespoke brackets, designed based on the swing door’s measurements. These act as templates to position the profiles so that the corners are perfectly 90 degrees,” explains Feltrin + Masarin.
“Then, we carry out glass assembly operations with the aid of a lifter.”
As a result of Feltrin + Masarin’s precision from beginning to end, the final product fits together perfectly.

The glass assembly operations are carried out with the aid of a lifter composed of a movable arm, a remote console to control the movements, and 4 suction cups that secure themselves onto the glass — the capacities vary from 125 to 2000 kg.
This is arguably the most challenging phase as it requires Feltrin + Masarin to handle heavy quantities of glass—often varying between 20 to 75 kilos a piece. However, first a thorough cleaning is carried out before 3M double-sided tape is placed on each profile, with the help of a guide roller.
Phase 4: packaging
The final phase is the packaging phase, which requires a final check on the swing door before being placed in a hermetically closed barrier bag to protect the door from humidity during overseas shipments.
The insertion of bags of dehydrated clay ensures the absorption of any remaining moisture and prevents the buildup of moisture during transport.
The door is finally placed in fumigated wooden crates, which helps to fend off mould and other parasites from the wood to ensure it doesn’t reform, and carefully labelled before shipping.
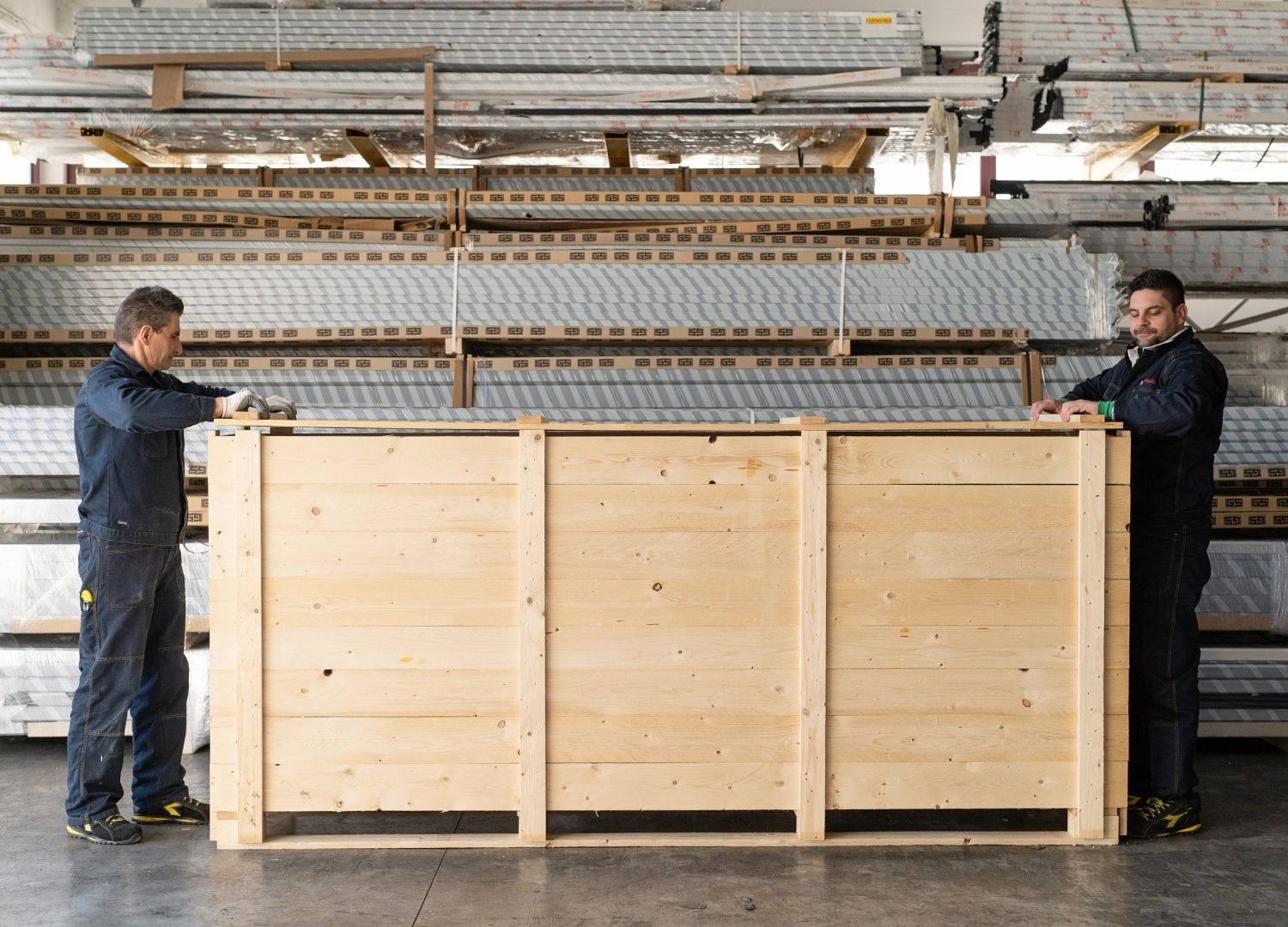
“We use closed cell polyethylene foam corners, which are affixed to the sides of the profiles to protect the corners from impact too,” says Feltrin + Masarin.
“It is the ideal material for the protection of painted and very delicate items against shocks given the high shock absorbing and anti-vibration capacity. Plus, it is 100% recyclable, light and does not release dust, which can in turn compromise the final quality of the product being received by our client.”