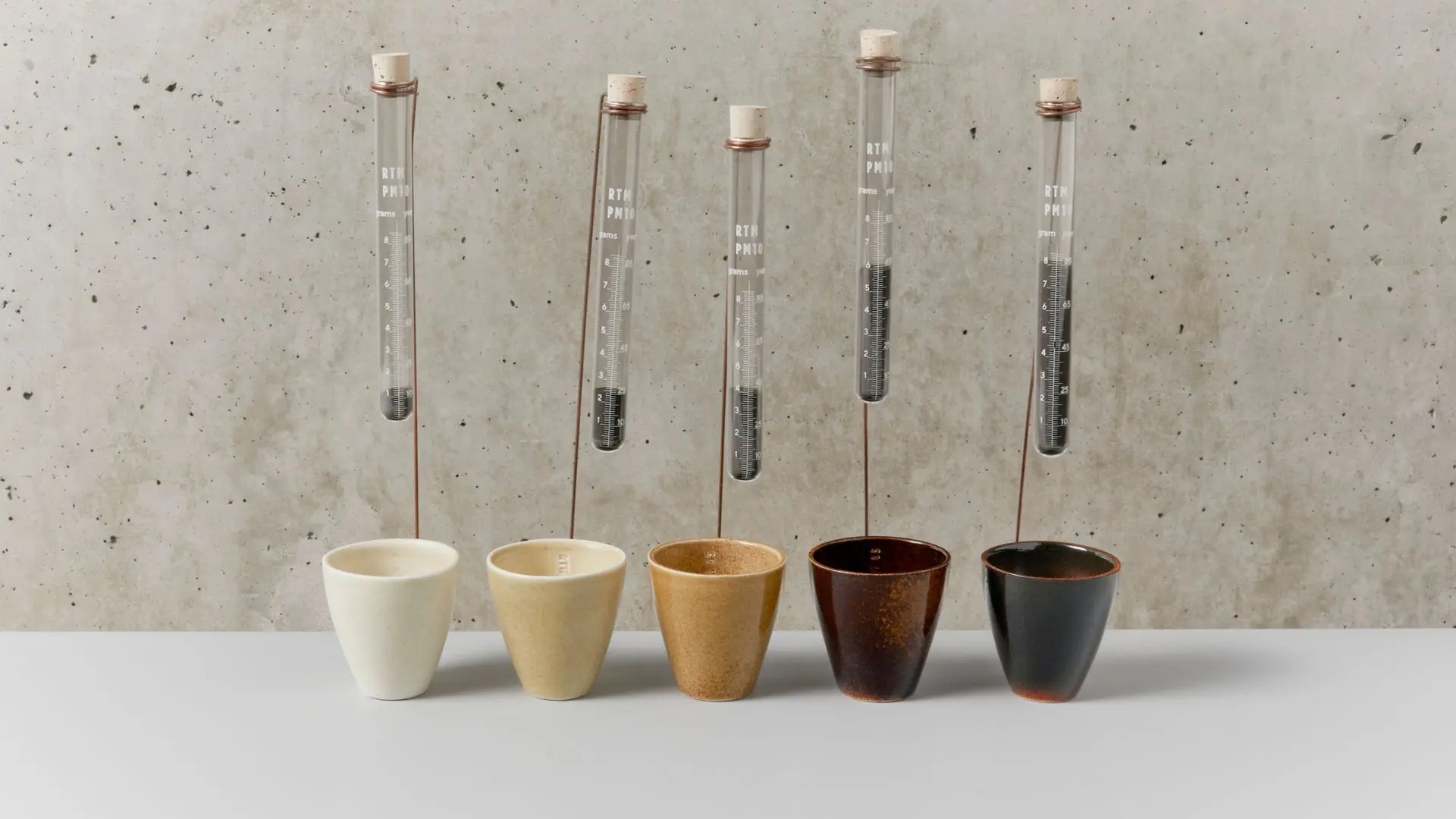
Join our Newsletter
Every week, get to know the most interesting Design trends & innovations
As the name suggests, explosive forming is a manufacturing technique that uses explosions to force metal into dies and molds. In place of a punch or press, explosives are typically either detonated underwater or in direct contact with the materials, releasing energy instantly so that an extremely high pressure with short duration occurs at the instance of explosion.
In order to perform the forming process correctly, it is necessary to precisely determine the proper amount of explosives.
In terms of the product or material being formed, this process is applied mainly to metals. However, as the process incorporates explosives and a die it also technically includes other materials such as concrete, ductile iron, fiberglass, and kirksite or epoxy, and concrete, all of which can be used to make the die. The explosive material is typically Trinitrotoluene (TNT), a mixture of acetylene and oxygen or Nitroglycerine.
The range of metals that can be used includes: aluminum and its alloys, stainless steels, magnesium and some of its alloys, titanium and its alloys with aluminum, vanadium and manganese, refractory metals, copper and its alloys, and special alloys such as stellite, iron-nickel, nickel-copper, chromium-nickel, and cobalt-iron. Carbon and low-alloy steels are less often used because they have low formability in dynamic conditions such as the ones created by explosive forces underwater.
It can be used for forming a multitude of different parts. These parts can vary on a scale that ranges from a few inches and up to 15 feet. Technically, there are no restrictions and the main limitations are the potential impact of detonation and the size of the holding tank.
Because of this flexibility, explosive forming has historically been employed in the aerospace industry for the prototyping of complex parts with complex shapes. It also lends itself to parts that are produced in small numbers or even unique productions.
Explosive forming only became popular in the mid-1950s, during a time when multiple aerospace companies in the United States were popping up that required it for the forming of complex curved aerospace components.
The process was especially important in the development of short-production-run missile components—particularly for the curved domes of missiles and rocket nose cones.
Not limited to aircrafts, other applications of explosive forming also include architecture, particularly useful when realising buildings that have a unique expression. Large metal panels with complex shapes can be made while maintaining sound mechanical properties.
[ Read more about Plastic Overmolding? ]
Whilst it might sound intimidating the process of explosive forming is very straightforward. In general, a die is manufactured according to the desired shape of the product. A metal sheet is placed onto the die, the die cavity is vacuumed and the assembly is placed underwater.
The forming part of the process takes place next, inside the water tank or ‘explosion’ tank where the die is placed. The workpiece is situated directly above the die and explosive material, or the TNT is placed above that. After detonation, an explosive charge pushes the sheet into the die to create the final product.
All manufacturing processes can be dangerous, but as you can imagine, one that uses controlled explosives can potentially be more so.
For that reason, it’s strongly recommended that explosive forming is managed by professionals who have an advanced understanding of explosive materials and their impact. It requires a controlled environment that cannot be replicated at home.
Several advantages to explosive forming include being able to produce virtually any shape in any size and obtain it without recourse to plant or machinery. Instead, a comparatively light forming tool consists only of a die that requires no foundations.
It can also be a relatively cheap process with savings due to the fact that there is no cost of presses, tooling, etc. The dies for stand-off operations are very often made from cheap cast materials such as epoxy or concrete. Explosives are not only powerful but also cheap, compared to many other types of energy.
However, explosive forming is not economically viable when a very large number of components is required because it can only be used to create one product at a time therefore can be time-consuming.
There are methods similar to explosive forming in the way they shape metals. Whilst completely opposite in the sense that it uses much lower temperatures and absolutely no explosive force, processes like cold metal forming and rolling, which both use low temperatures to shape metal; hydroforming that uses fluid to press room temperature materials into a die; and press forging, which works by slowly applying continuous pressure to materials.
[ Read also What is cold forming? ]
Explosive forming is far from sustainable as it requires energy to create the die, the container and it uses water. The main source of energy during the manufacturing process is also TNT which is not renewable and contains chemicals that pollute the environment.
There are several resources that are useful when it comes to building your knowledge around explosive forming. If you want to learn more check these out:
• A visual demonstration of explosive forming and its impact
• A detailed and annotated diagram of explosive forming explaining its various components
• A study into explosive forming processing methods and aerospace structures
• A paper detailing the science of explosive forming