

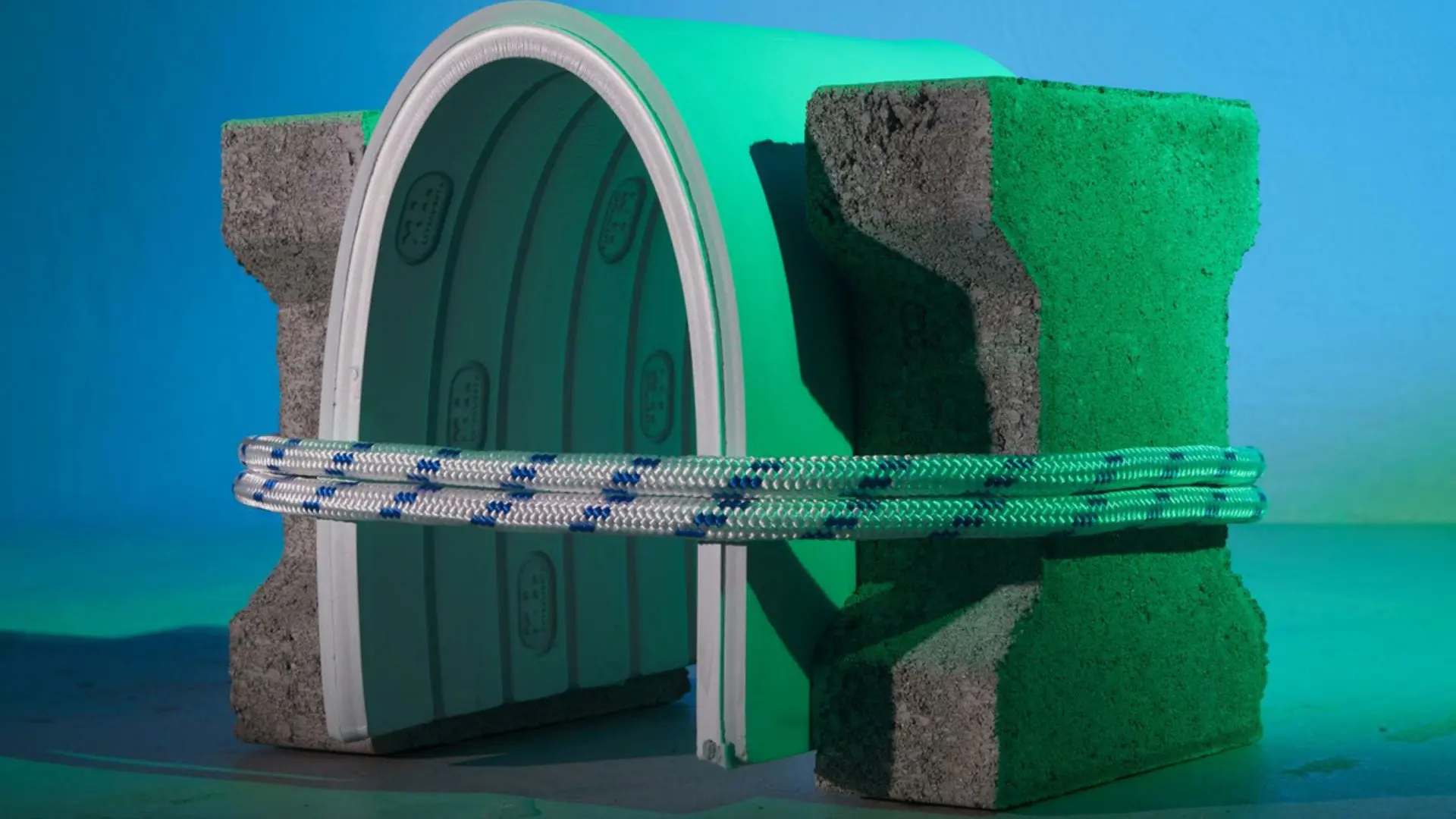
A one-of-a-kind garden where balance and paradox reign

10 of the best autism-friendly design projects
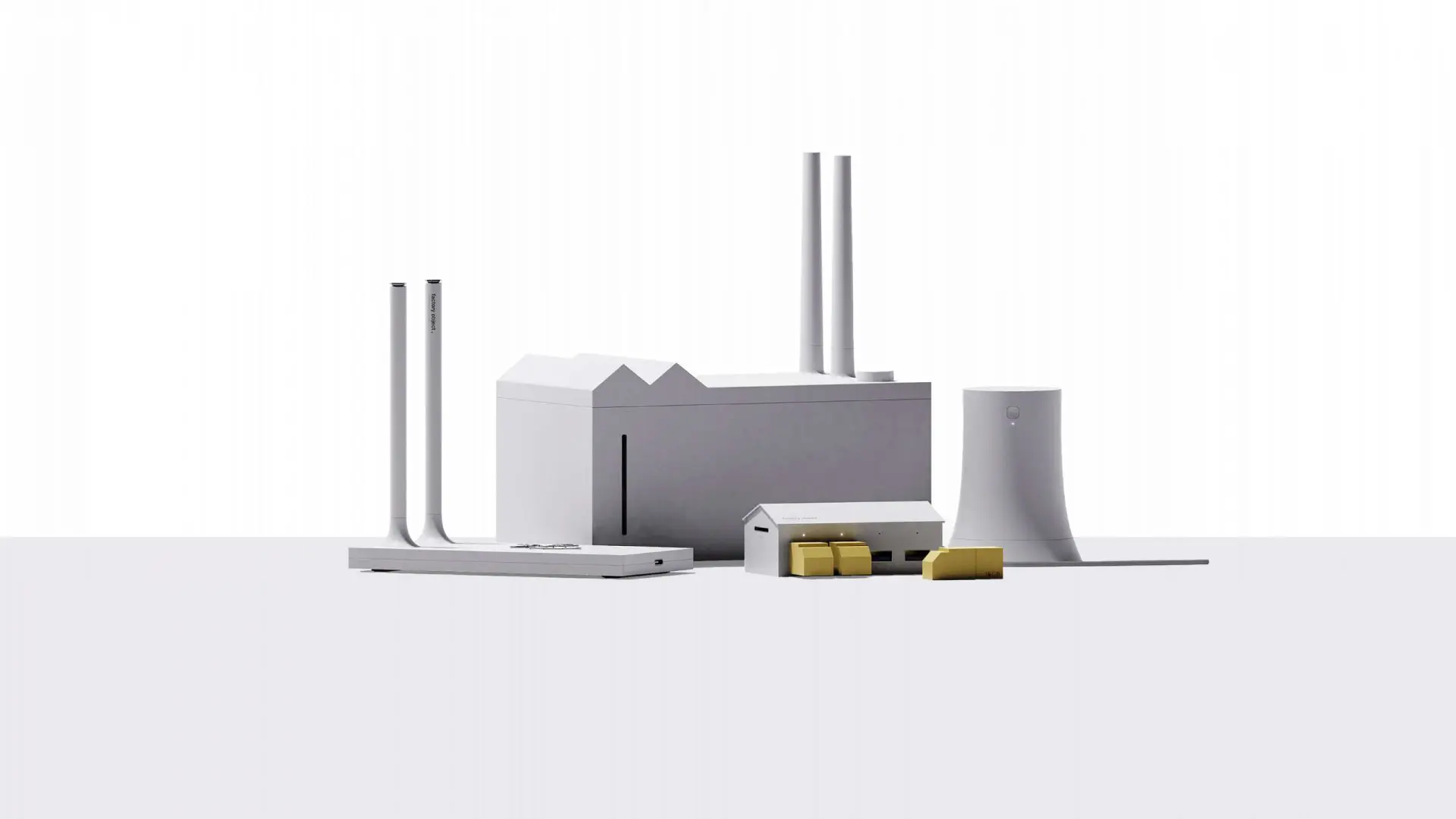
The piece is based on the creation of a new cement-like material that uses barley, which is filtered and removed from the liquid after giving flavour to the beer. This waste is bound with cement, generating an inorganic-organic composite, which is lighter and with better capacities than normal cement.
“I realised that barley malt is almost the only waste produced from the process, along with some little leftovers of the yeast,” she explains. “I was attracted by this residual “organic material” and I decided to try to give it a second life.”
Looking for more sustainable objects? Don’t miss the chance to take a deep-dive into The Ocean Cleanup and discover a selection of products, all made by upcycling ocean plastic!
Around the world, different ancient civilisations have developed building techniques that use organic products. For example, in China 500 CE, sticky rice soup was mixed with slaked lime to make an inorganic-organic composite mortar that had more strength and water resistance than lime mortar.
Nowadays there’s new versions of this technique that use agricultural waste instead of newly grown rice products. Some of these variations extract silica from barley and rice husk, creating an agro-silica-a nanoscale additive capable of improving strength, workability and fire proofing.
Similar to rice cement, Maymó began researching ways she could create composite material from barley, like waste bricks or other inorganically bonded natural composites.
“Among other improvements such as higher thermal insulation and strength, these new formulas help reduce the large carbon emission produced by traditional cement manufacturing,” Maymó says. “I was glad to find out many of these mixtures resulted in carbon negative materials.”
The resulting material is formed during a process known as curing, defined as providing adequate moisture, temperature, and time to allow the concrete to achieve the desired properties. It involves an important chemical reaction between the water and cement, which binds to aggregate and enable hydration while releasing heat.
After drying the barley to prevent mould, Maymó combined the material with cement and water, experimenting with different formulas to understand the impact each component had on the final product. Over the 4-6 week period, it can take for the material to achieve its final strength, controlling temperature and humidity is essential.
“When there is too much water in the concrete there is greater shrinkage with the possibility for more cracks and reduced compressive strength,” she explains. “If there is too little water, or you allow the water to evaporate too quickly, the chemical cure will not be complete and the concrete will become weaker.”
It took several weeks and multiple tests before Maymó obtained a sample of a small brick with the desired strength and properties. She then added a natural pigment and tried out various colour tests before achieving the muted hue seen in the final piece.
“I had some initial setbacks with the production of the moulds for the blocks,” she explains. “At first the acrylic moulds were not strong enough so the weight of the material was deforming the mould.”
“After strengthening these with an outer extra layer of wood, I proceeded to build the final blocks on scale 1 to 1. After a 6 week period, I considered they had achieved the desired strength and resistance.”
“I proceeded to scale up a bit and produced a few successful samples at a slightly larger scale.”
The final product is a minimalist take on a totem-style pedestal, combining a set of modular blocks made using this barley-cement composite. These blocks, which Maymó intends to be used in various configurations, are combined with layers of bronze glass in contrast with the visual heaviness of the stacked bricks.
“That is why the piece is called Malta I, denoting the possibility of creating an infinite number of different Malta pieces.”
“The result is a composition in which the formal simplicity hands over the prominence to the materiality and contrast between the elements.”
Sometimes innovative materials are simpler than you expect. This sustainable SOAPBOTTLE packaging is made from soap thus being biodegradable and zero-waste!
Every week, get to know the most interesting Design trends & innovations