3D printing was used to build microstructures of this aluminum chair
The Aluminum Gradient Chair by Joris Laarman is part of the permanent collection of the National Gallery of Victoria as well as the Vitra Design Museum.
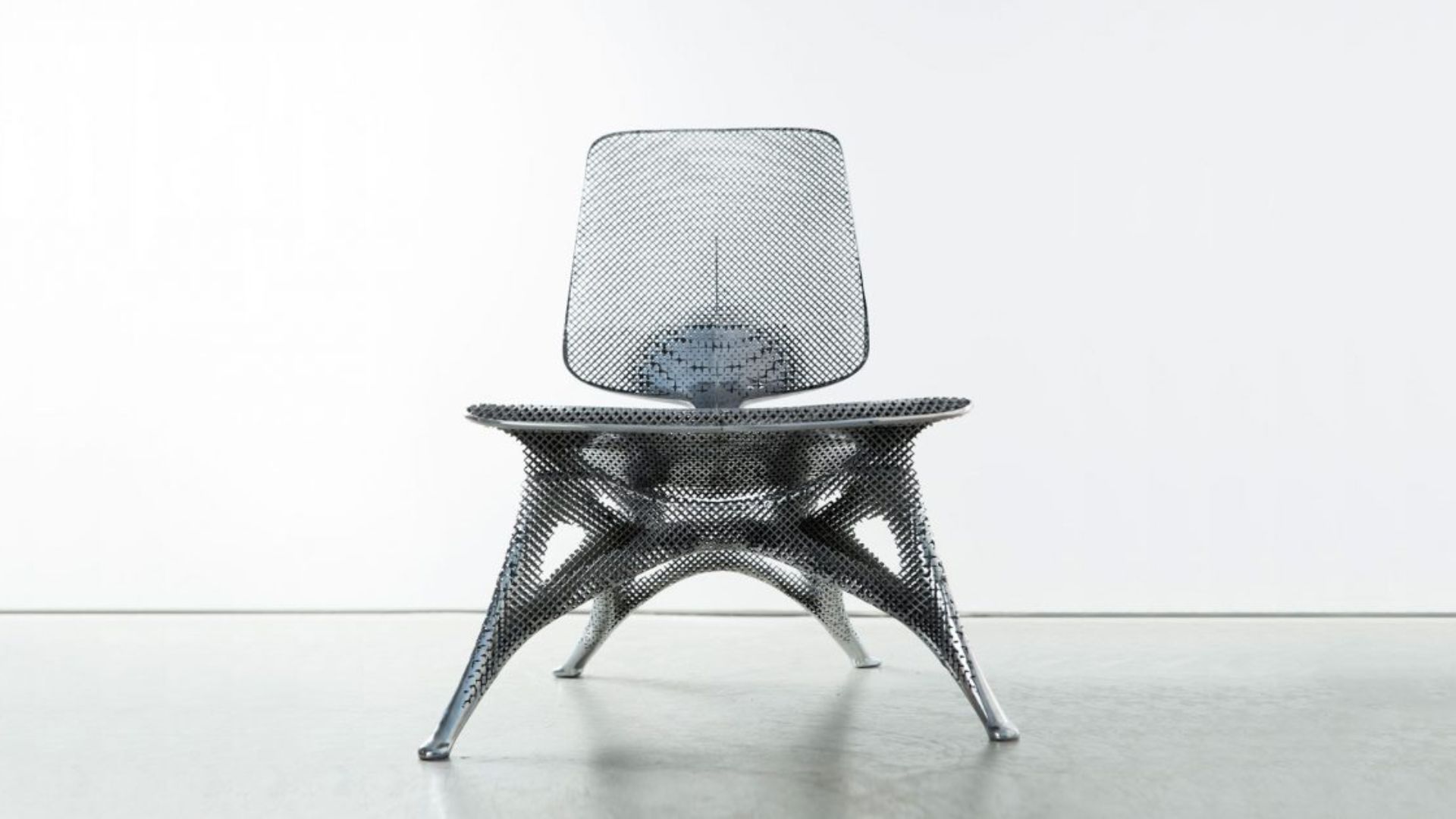
Playing with ideas is an important way of developing them to their full potential and at Joris Laarman Lab, that’s a central activity of their daily practice (3D printing). Their most recent piece to make a splash is a 3D-printed Aluminum Gradient Chair that made its debut at the Friedman Benda Gallery in New York as part of a solo show entitled Bits and Crafts.
The Lab, which was founded in 2004 by Joris Laarman and Anita Star, is located in the fruitful design environment of the Netherlands and has been on the 3D printing news radar for quite some time now.
The piece, “Aluminum Gradient Chair,” was created as the result of extensive 3D printing experimentation with the possibilities presented by microstructures as a means of form finding.
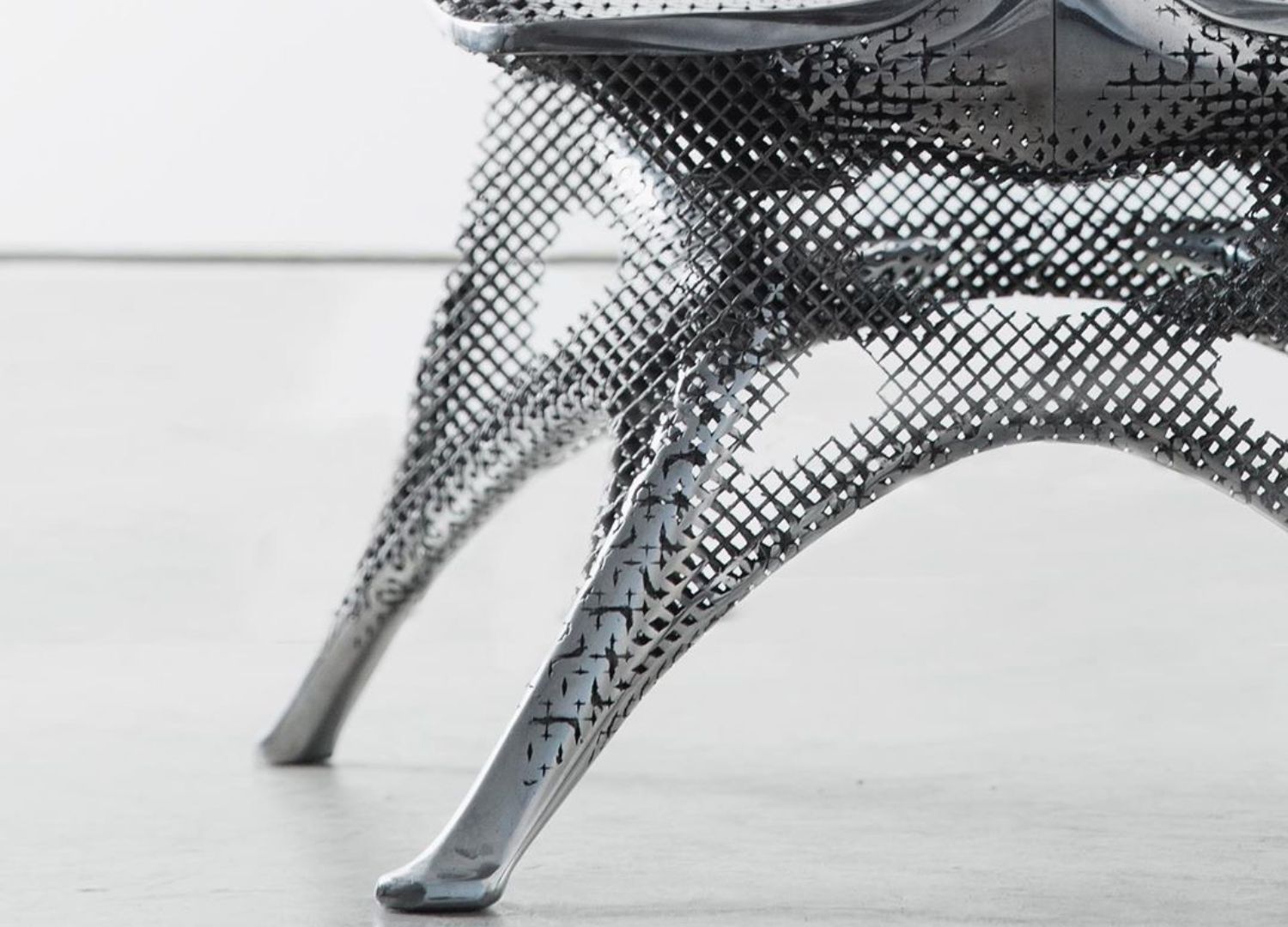
Microstructures are, as the name implies, the very small-scale structures that are found in any particular material and can have very profound impacts on the material’s characteristics in terms of strength, hardness, corrosion resistance, and others.
Rather than keeping these microstructures secret, Laarman Labs decided to reveal them in the form used to create the chair, somewhat akin to demonstrating the code behind the material. After all, it is the exact nature of these microstructures that make the material, in this case aluminum, naturally perform in such a way as to make the chair possible.
Rather than seeing the material as something to be overcome in order to create a form, the most basic nature of that material was used and revealed as part of the chair’s final state. This is more than just a novel trick, but rather speaks directly to the manufacturing process used to create the furniture piece.
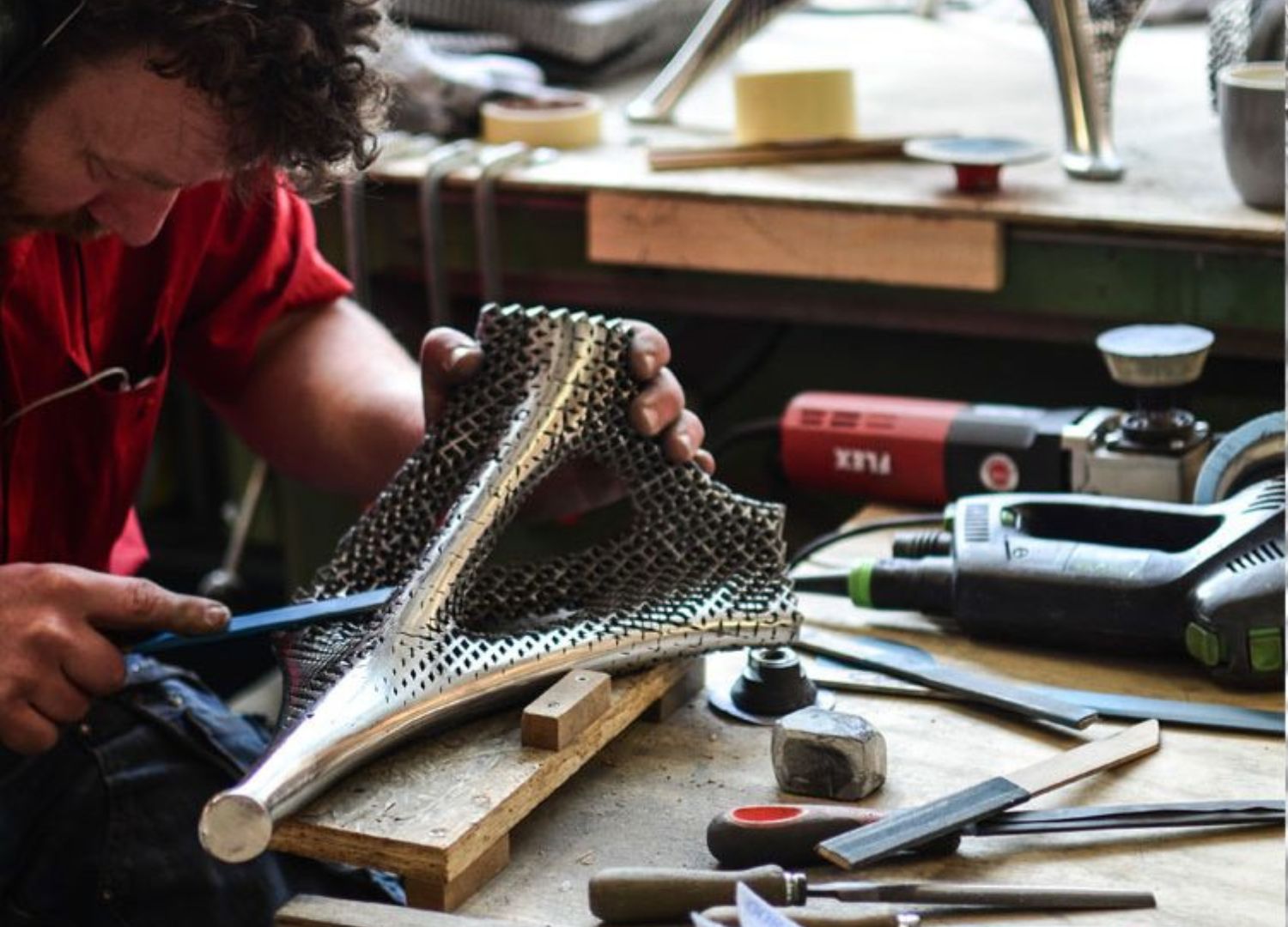
Just as molecular accretions serve to build up the microstructures of a chair, 3D printing was used to build those microstructures into the overall form. The team used laser sintering to create the structures that make up the chair, which allowed for the creation of a supremely lightweight and yet solidly functional piece.
In addition, the attention paid to the structure of the individual units making up the chair greatly reduced the amount of material that would have otherwise been necessary had the team been focused purely on the exterior form.
As each of the cells of the chair is open, the tone of the chair shifts with the gaze of the viewer, adding life and vivacity to the monochromatic object. In other words, the tone and shades are created as a result of the structure, much like structural color is built in to the wings of a butterfly or the flashy chest feathers of a ruby throated hummingbird.

Rather than being an external application, they are generated directly and naturally as the result of the structure itself, a perfect marriage of surface and form. As is befitting such a creation, the 3d printed Aluminum Gradient Chair is now part of the permanent collection of the National Gallery of Victoria as well as the Vitra Design Museum.