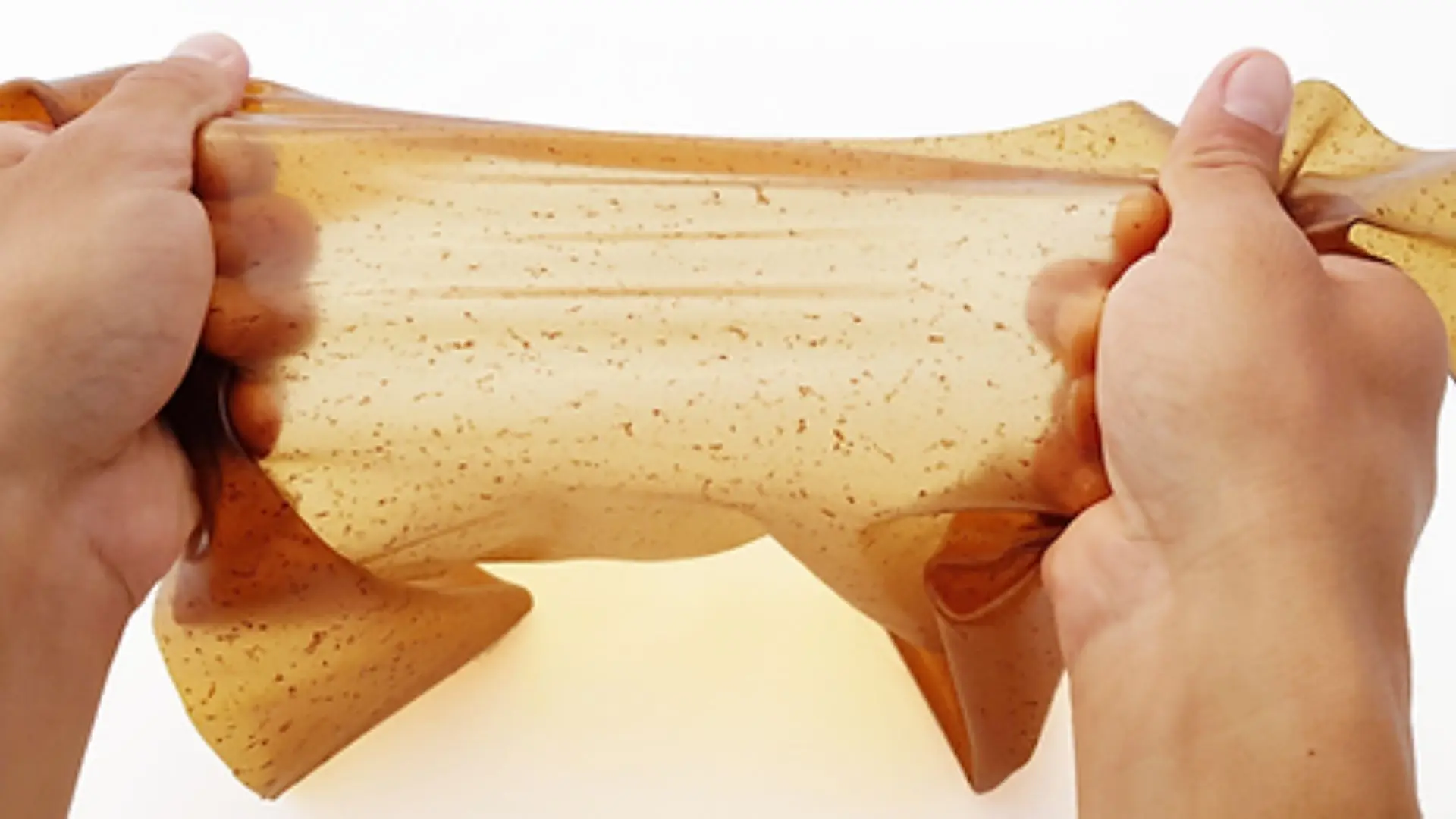
Despite modern decarbonization efforts, such as substituting Portland clinker with supplementary materials and exploring alternative binders, concrete accounts for approximately 7.5 per cent of global anthropogenic CO₂ emissions and poses an unignorable environmental challenge. A new patented process entitled the Cambridge Electric Cement in the global effort to achieve net zero emissions powerfully addresses this issue.
Ideated by Cyrille F. Dunant, Shiju Joseph, Rohit Prajapati, and Julian M. Allwood, the trailblazing team of researchers from the University of Cambridge, the transformative method to produce extremely low-carbon concrete at scale involves the recycling of old cement from demolished buildings by heating it and reactivating the compounds within it followed by the use of electrically-powered arc furnaces borrowed from the steel industry.

The engineers’ innovative approach simultaneously addresses both of the major sources of carbon emissions–the chemical reaction as limestone is turned into new cement and the firing of fuels to power the high-heat kilns needed for that process. What they have discovered is that used cement can effectively replace lime flux in steel recycling thus eliminating the production of waste slag. This breakthrough formula results in recycled cement that can be used to create new concrete.

What does the process entail? Following any building’s demolition, its concrete gets crushed to the point where the cement can be separated from the aggregates. The used cement is then taken to a steel furnace and used in place of lime as the “flux,” the cleaning agent used in the recycling process to remove impurities from the molten metal.
The flux is combined with the impurities to form slag, a byproduct that rises to the top of the molten steel and can be easily detached and removed. If the cement-based slag is removed and quickly cools down, it turns into high-quality Portland cement, the carbon-intensive component of concrete.

Since the Cambridge Electric Cement has the same chemical composition, this recycled cement is expected to be as durable as any other cement in the UK. The fact that it uses existing processes, equipment, and standards–without any substantial additional costs for either the concrete or steel industries–is undoubtedly another added benefit.

Created to commercialize the inventive product, the team’s private company Cambridge Electric Cement has been scaling rapidly, and the engineers claim they could be producing one billion tonnes of zero-emissions cement per year by 2050. Cambridge Electric Cement is a collaboration between the Universities of Cambridge, Warwick, and Imperial College London and is funded by EPSRC.
The formula can lead to the creation of cement with minimal emissions and zero waste. In of itself, this has the potential to revolutionize cement production by reducing the need for limestone mining and eliminating the use of questionable additives like heavy metal-laden fly ash as filler for concrete. A sustainable, zero-landfill future just might be on the horizon.