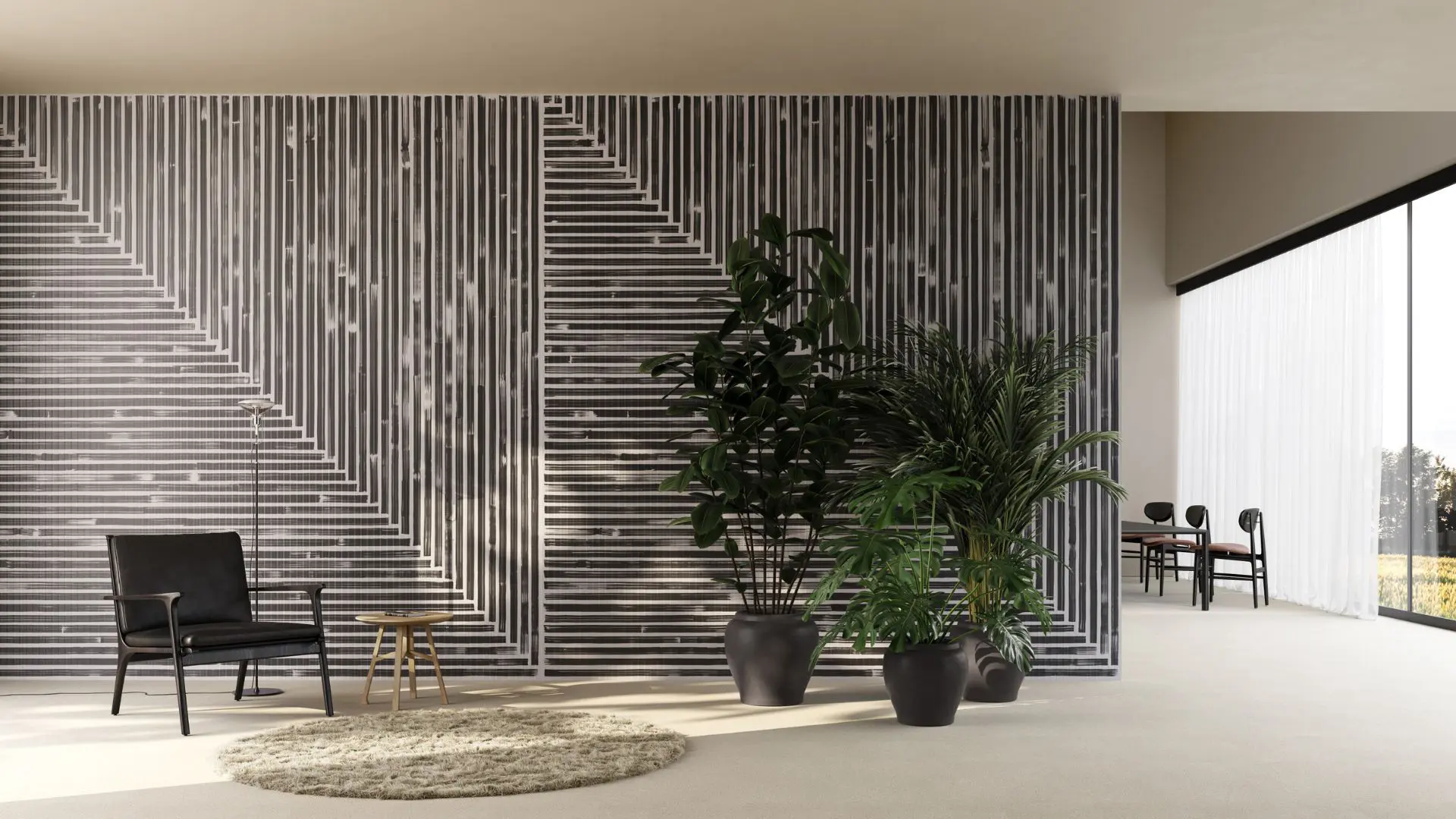
Join our Newsletter
Every week, get to know the most interesting Design trends & innovations
“Today we mark an important milestone, another concrete achievement that demonstrates our commitment to decarbonizing the ceramic sector. This is a unique and cutting-edge project of global significance, opening new prospects for hard-to-abate manufacturing, proving that it can be done,” declares Federica Minozzi, CEO of Iris Ceramica Group.
“The testing phase will help us refine the production process, after which we will move to the next phase, allowing us to gradually increase the percentage of green hydrogen up to 50% with the production system that Edison Next is custom-building for us. This is a highly valuable partnership, and we are proud that this milestone is the result of a team effort across the entire supply chain, a virtuous example of integrated sustainability. We hope that other companies will follow our path to truly create a system and become a driver of change at the national level and beyond,” concludes Minozzi.
To launch this initial phase, several preparatory activities were conducted: civil works to prepare the area, installation of the blending unit (which mixes natural gas with green hydrogen), and the creation of all necessary connections between the different machines. Additionally, a 1.3 MWp photovoltaic system was installed, adding to the existing 2.5 MWp system.
The pilot H2 Factory production plant, which began operations in May 2024 to facilitate the testing phase, includes two temporary electrolyzers with a total power of 120 KW electric, powered by renewable energy. These electrolyzers, housed within a container, can produce a total of 20 cubic meters of green hydrogen per hour, enabling the new “hydrogen-ready” next-generation kiln to be fueled with a green hydrogen blend of up to approximately 7%, a percentage set to increase once the permanent plant is installed.
The objective of this first phase is to refine the use of technology for producing ceramic slabs using green hydrogen and to verify the material’s behavior during the firing process. This will allow for the industrialization of green hydrogen production while ensuring the qualitative, technical, and aesthetic excellence that Iris Ceramica Group is known for. The 4D Ceramic, produced by the H2 Factory, is the Group’s flagship product, showcasing the beauty and nobility of this natural material, which serves the high-end furniture market.
In parallel with the testing phase, Edison Next will begin the necessary activities to install the final system in the coming months. This system, a green hydrogen production plant via electrolysis with a capacity of 1 MW, will produce about 132 tons of green hydrogen per year. This will fuel the kiln with a blend of methane and green hydrogen of up to approximately 50%, immediately replacing about 500,000 cubic meters of methane gas per year and avoiding the emission of approximately 900 tons of CO2 annually into the atmosphere.
The green hydrogen production system being developed by Edison Next for H2 Factory is designed to allow for a further doubling of green hydrogen production, which will enable the operation of a new 100% hydrogen kiln currently under study.
Open full width
Close full width