Design meets archaeology in Roberto Sironi’s RUINS

A deep-dive into Italian designer Roberto Sironi’s series RUINS, an in-depth research-based project that reinterprets the archaeology of architecture through fragments and contemporary elements using casted bronze, marble and glass.
Roberto Sironi lives and works in Milan. He studied Industrial Design at Politecnico di Milano, and worked in various design studios that led him to develop his design approach. Since 2014, he has combined his own design practice with teaching and research in the Design Department of the Politecnico di Milano, and in 2015 he founded his own studio.
Sironi’s Milan-based studio has a practice-based research approach, where the artefacts produced are intended as narrative mediums. The RUINS project well represents this kind of approach: a dense and articulated thought, built through in-depth research, which becomes tangible through the matter transformation and manipulation, with a precise choice of processes, materials and finishes to obtain artefacts conceived as the research outcomes.
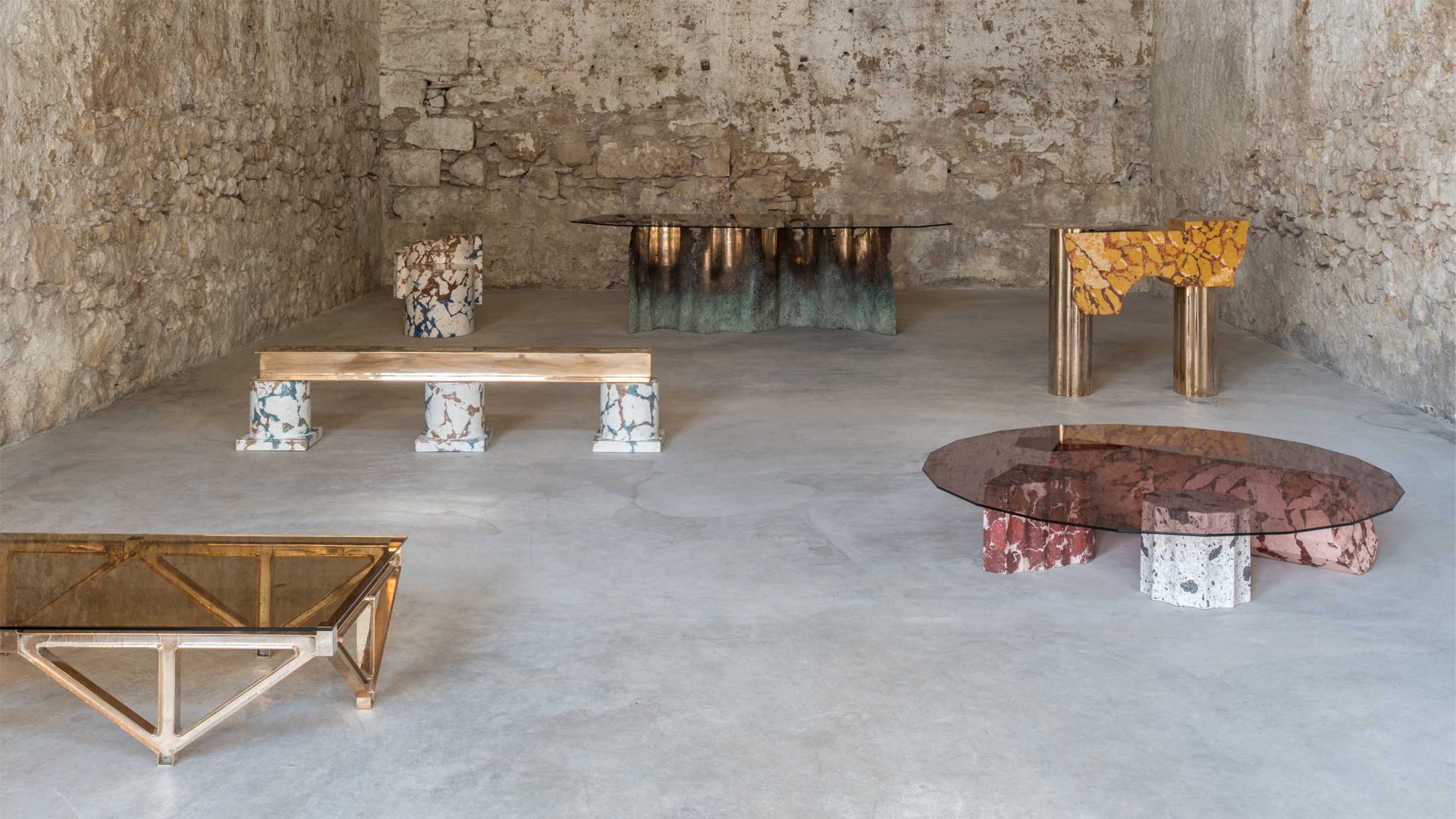
“RUINS is a speculation on the archaeology of architecture: the constructive elements of the classical era are overlapped with rudiments of the industrial era with the aim to create post-archaeological ruins, elements freely deconstructed and reconstructed, a kind of simulacra.” explains Roberto.
“[This project] is the creation of contemporary, post-archaeological ruins, it’s a sort of fiction. So I needed to use two functional materials on an aesthetic and conceptual level, capable of incorporating a series of information and values to be transferred to the public.”
In RUINS two materials are used: the parts belonging to industrial archaeology are transposed into bronze through the lost wax casting technique, while those that refer to classical archaeology are made in Marmo di Rima, a craft technique created in Italy in the mid-nineteenth century with the aim of imitating natural marble.

“I used two different techniques: the first is the lost-wax casting, thanks to which corrugated sheets metal, reticular structures and double T-beams are transformed from iron into bronze, and then mirror-polished and patinated, as in the case of the TURIN table.”
“The other is Marmo di Rima, a decorative technique born in the second half of the nineteenth century in Rima (Italy) to simulate marble, and which is composed of a mixture of gypsum, organic glue, water and pigments.”
“While for the bronze I already had an excellent experience, in the case of Marmo di Rima it was a leap in the dark.” Roberto says.
Discover more studios reviving craft techniques into their work, don’t miss Ukrainian ancestral craftsmanship revived in lamp collection SONIAH by Victoriya Yakusha.
Asking Roberto about his process to get to the final result, he gave us his lost wax casting technique recipe:
“1. The corrugated sheet metal was brought to the foundry and cut into 4 parts to facilitate the molding process
2. Creation of a model in plaster and silicone: the first negative
3. From the negative to second positive made in wax, with a thickness of about 5 mm
4. The positive wax models are retouched by hand, applying liquid wax with a brush to create the texture
5. Application of sprud-rods, channels made of wax applied to direct the melted bronze during the casting
6. Coverture of the waxes with a mixture of refractory material and plaster, creating a cylinder: the second negative
7. The refractory cylinder (one cylinder for each of the 4 parts of the sheet) is heated in the ovens for twelve days up to 650° to eliminate water and to synthesize the refractory material
8. Casting at a 1200°, the bronze runs in the void left by the channels, filling the interstice left by the lost wax

9. Extraction of the bronze from the refractory mold
10. The bronze pieces are washed with high-pressure water and the bronze channels are removed
11. The 4 parts are welded and chiseled
12. The upper part is mirror-polished patinated
13. The lower base is heated and then treated with a brush to apply a patina called Bronze Green which is obtained from the chemical reaction between bronze and the substances applied.”

“The innovative technique used in this process is the application of the wax on the positive model: once heated to make it liquid, the wax is worked to obtain the desired density and then applied by hand with a brush.
Through the lost-wax casting technique it is possible to achieve a perfect adherence between the initial model and the final work, in terms of shapes fidelity and detailed textures.

The bronze casting also allows you to aesthetically manage the surface of the material: with the application of the patinas it is possible to treat the material in terms of color, by applying a series of chemical reagents that accelerate the natural ageing process of the bronze.”
The final result is a set of colorful sculptural pieces conceived as fragments of contemporary ruins. These fragments are reshaped in order to acquire a new functional use as well as a completely different aesthetic.
Are you into unconventional processes of production? Head to Studio ThusThat made this lamp using waste products from copper.
